Our Brazing and Soldering Services
Automated brazing equipment is specialized equipment used in the process of brazing, where two or more metal parts are joined together using a filler material that melts at a higher temperature than solder but lower than the melting point of the base materials.
The equipment automates the brazing process with robotics and controllers while ensuring precision, repeatability, and high-quality joints for manufacturing applications.
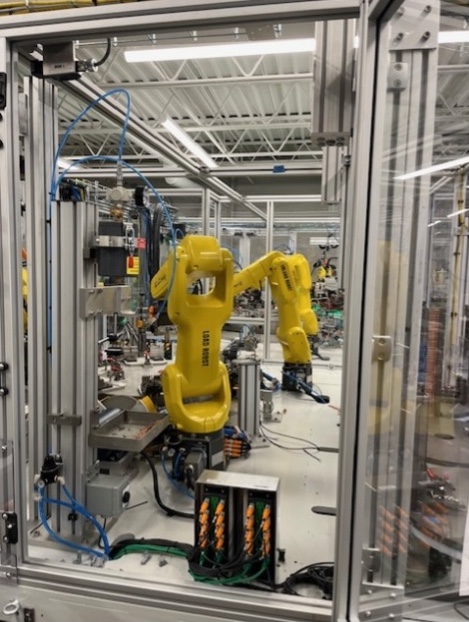
What is Brazing?
Brazing is a process where two or more metal parts are joined and bonded using a filler metal. The filler metal that has a lower melting point than the base metals that are being joined. Unlike welding, brazing does not melt the workpieces themselves; instead, the filler metal is heated above its melting point and flows into the joint by capillary action, creating a strong bond as it cools and solidifies. This process is used in industries like automotive, aerospace, and HVAC.
What is the difference between brazing and soldering?
Brazing and soldering are both methods of joining metals using a filler material, but they differ in strength and in temperature:
- Temperature: Brazing is performed at a much higher temperature, typically above 450°C (840°F), while soldering occurs below that threshold. The higher heat in brazing creates much stronger joints.
- Strength: Brazed joints tend to be more durable and resistant to mechanical stress and high temperatures, making them more suitable for industrial applications, whereas soldered joints are used for more intricate and delicate work like electronics.
- Filler Material: Brazing uses a brass or silver-based filler that flows into the joint, while soldering usually employs a softer lead- or tin-based alloy.
- Bonding Mechanism: Brazing forms a stronger metallurgical bond than soldering, which just holds the metals together without significantly altering their structure.
Brazing and Soldering Benefits
Cost Savings
- Labor Savings: Automation reduces the need for highly skilled manual labor, thereby saving on labor costs and minimize the risk of human error.
- Material Savings: Automation equipment can be optimized to use the proper amount of filler and flux material, thereby reducing waste and material costs.
Quality
- Repeatability and Precision: Automated systems ensure that each joint is created under the same conditions leading to reduced variation and consistent quality.
- Reduced Human Error: Automated systems eliminate the variability in manual brazing, such as inconsistent temperatures, differences in technique, human fatigue, and handling errors.
Increased Throughput
- Faster Production: Automation brazing equipment is generally much faster than manual brazing. The ability to handle multiple joints and/or parts simultaneously can increase throughput and increase overall efficiency.
- Consistency: Automated systems increase throughput and is achieved due to minimal downtime and reduced operator involvement.
Improved Safety
- Reduced exposure: Brazing often involves potentially dangerous fumes, high temperatures and hazardous materials. Automation minimizes the direct involvement of operators enhancing worker safety.
- Controlled Environment: Automated brazing equipment can be integrated into controlled environments such as furnaces and robotic cells which can regulate temperature, gas flow , reducing risks of accidental exposure.
Scalability
- Integration with other systems: Automated brazing/soldering systems can be integrated with other systems (inspection, assembly, or packaging) allowing manufacturers to create streamlined production lines.
- Scalable Production: As demand grows, automated equipment can be easily scaled to accommodate higher volumes or different SKU’s, providing flexibility for future production needs.
Brazing and Soldering Experience
Our team has decades of experience in designing automated brazing and soldering systems.
Ready to Innovate?
If your company is looking to modernize its operations, improve efficiency, and enhance product quality, we are here to help. Contact 4D Systems today to learn more about our custom engineering solutions and how we can transform your manufacturing processes.